بررسی خواص فولاد Crofer 22APU پوشش داده شده با Co/y2O3 به روش آبکاری الکتریکی با جریان مستقیم
فولاد Crofer 22apu
فولاد زنگ نزن فریتی Crofer 22 APU به عنوان ماده ای مناسب. برای ساخت اتصال دهنده در پیل های سوختی اکسید جامد مورد استفاده قرار می گیرد. از مشکلات مهم این فولاد، افزایش مقاومت الکتریکی و تبخیر کروم از آن در دمای بالاست. به منظور رفع این مشکلات می توان از یک لایه پوشش محافظ روی آن استفاده کرد. در این پژوهش، از پوشش کامپوزیتی کبالت/اکسید ایتریم متشکل به روش آبکاری الکتریکی استفاده شد. سپس مقاومت به اکسیداسیون و مقاومت الکتریکی نمونه های پوشش دار و بدون پوشش مورد بررسی قرار گرفت.
به منظور بررسی اثر اکسیداسیون روی ریزساختار و ترکیب نمونه ها، از آنالیزهای میکروسکوپی الکترونی روبشی و پراش پرتو ایکس استفاده شد. نتایج نشان داد نرخ اکسیداسیون نمونه بدون پوشش پس از 500 ساعت اکسیداسیون در هوا. در 800 درجه سانتیگراد حدود چهار برابر نرخ اکسیداسیون نمونه پوشش دهی گردید. تشکیل ترکیبات اسپینلی Co3O4 و MnCo2O4 روی نمونه پوشش دار هدایت الکتریکی را بهبود داد. مقدار مقاومت ویژه سطحی نمونه پوشش دار و بدون پوشش بعد از 500 ساعت اکسیداسیون. به ترتیب برابر 15/8 و 25/9 میلی اهم بر سانتی متر مربع اندازه گیری شد.
فولاد Crofer 22apu
مقدمه
پیل سوختی اکسید جامد (SOFC) یک وسیله تبدیل انرژی است. که از طریق ترکیب الکتروشیمیایی یک سوخت و یک اکسیدان در امتداد یک الکترولیت اکسیدی هدایت کننده یونی، تولید الکتریسیته و گرما می کند. در کاربردهای عملی SOFC، تعداد زیادی از سلول های واحد نسبتاً کوچک به یکدیگر متصل می شوند. تا جریان الکتریسیته لازم را فراهم کنند. پیل های منفرد توسط یک جزء سازنده به نام اتصال دهنده بین سلولی به یکدیگر متصل می شوند. تا یک بدنه واحد را تشکیل دهند.
این اجزاء علاوه بر اتصال الکتریکی، به صورت یک سد فیزیکی مانع از هر گونه تماس بین اتمسفرهای احیایی و اکسیدی می شوند. اتصال دهنده ها باید دارای هدایت الکتریکی خوب. نفوذ ناپذیری عالی، انطباق ضریب انبساط حرارتی با الکترودها و الکترولیت. مقاومت به اکسیداسیون خوب، قیمت پایین و در عین حال شکل دهی و ساخت آسان باشند. با کاهش دمای کاری سیستم SOFC به 800 -600 درجه سانتی گراد مواد فلزی به عنوان مواد مناسبی برای ساخت اتصال دهنده مطرح شدند.
فولاد زنگ نزن فریتی از بیشترین پتانسیل برای کاربرد به عنوان مواد اتصال دهنده در SOFC برخوردارند. در بین فولادهای زنگ نزن فریتی، Crofer 22APU به دلیل تشکیل SOFC روی اکسید کروم. از ضخیم شدن پوسته اکسید کروم جلوگیری کرده و باعث بهبود خواص مانند افزایش مقاومت به اکسیداسیون و هدایت الکتریکی فولاد می شود. با وجود این، لایه اکسید اسپینل منگنز- کروم از رشد لایه اکسید کروم بطور کامل جلوگیری نخواهد کرد.
این امر باعث ایجاد دو مشکل مهم در سیستم SOFC می شود. 1-افزایش مقاومت الکتریکی 2-مهاجرت اجزای کروم دار اتصال دهنده از طریق لایه اکسیدی به سمت کاتد. که می تواند باعث تخریب کاتد و نیز کاهش میزان کروم آلیاژ اتصال دهنده شود. که هر دو این عوامل می توانند روی عملکرد پیل تأثیر منفی داشته باشند. به همین دلیل لازم است که از یک پوشش محافظ های استفاده شود.
پوشش های مورد استفاده برای اتصال دهنده های بین سلولی در SOFC به سه گروه عمده تقسیم می شوند. پوشش های اکسید اسپینل مانند 3O4(CoMn)، 3O4(Mn،Cr) و 3O4(Mn,Cu)، پوششهای پیروسکایت مانند MnO3(La,Sr)، C0O3(La,Sr) و CrO3(La,Sr) و پوشش های اکسید عناصر راکتیو. عناصر راکتیو شامل عناصری از قبیل هافنیم (Hf)، زیرکونیوم (Zr)، ایتریم (Y) و لانتانیم (La) هستند. که قابلیت بسیار بالایی برای ترکیب شدن با اکسیژن و تشکیل اکسید دارند. پیوند این عناصر با اکسیژن بسیار قوی است.
در بین پوشش های اعمالی روی اتصال دهنده های فلزی، کبالت که در دماهای بالا به اکسیدهای اسپینل آن تبدیل می شود. به عنوان یکی از قابل قبول ترین پوشش ها معروف است. با وجود این دستیابی به یک پوشش مؤثرتر با یک روش مناسب روی این اتصال دهنده ها. برای دستیابی به مقاومت به اکسیداسیون بالاتر و هدایت الکتریکی بهتر در مقایسه با اسپینل های کبالت ضروری است. یک روش مؤثر برای اعمال پوششی مطلوب تر، ترکیب اسپینل های کبالت با عناصر راکتیو در یک پوشش است. این روش در تحقیقات سایر محققین نتایج مطلوبی داشته است.
فولاد Crofer 22apu
اکسید عناصر راکتیو نفوذ سربالایی کروم را آهسته کرده و چسبندگی پوسته اکسید کروم را افزایش می دهند. اما تبخیر اجزای کروم دار را کاهش نمی دهند. از طرفی اکسیدهای اسپینلی می توانند مقاومت الکتریکی و نیز تبخیر کروم را به طور موفقیت آمیزی کاهش دهند. روش های مختلفی برای رسوب کبالت روی اتصال دهنده های داخلی در سیستم SOFC مورد استفاده قرار گرفته است. در بین این روش ها آبکاری الکتریکی یک روش پوشش دهی ساده و ارزان است. یک مزیت مهم این روش فراگیر بودن آن است. به طور مثال با این روش می توان ذرات فاز ثانویه غیرهادی را به یک زمینه فلزی به صورت یک پوشش یکنواخت پیوند داد.
فولاد Crofer 22apu
2-مواد و روش تحقیق
در این تحقیق از فولاد زنگ نزن فریتی Crofer 22 APU ترکیب شیمیایی آن در جدول (1) آورده شده است. عنوان زیر لایه برای پوشش دهی به روش آبکاری الکتریکی با جریان مستقیم استفاده شد. از این فولاد قطعاتی به ابعاد 10×10×2 میلی متر تهیه شد. نمونه با کاغذ سنباده SiC تا شماره 2500 پولیش و در استون با دستگاه آلتراسونیک چربی گیری شدند. برای بالا بردن اکتیویته سطح و چسبندگی پوشش، نمونه ها به مدت دو دقیقه. در محلولی شامل پنج درصد وزنی اسید نیتریک و 25 درصد وزنی اسید کلریدریک قرار گرفتند.
سپس نمونه ها در الکترولیتی حاوی 90 گرم بر لیتر CoCl2.6H2O و 90 میلی لیتر بر لیتر HCl 37% آبکاری شدند. تا لایه نازکی از کبالت روی سطح نمونه ها تشکیل شود. این عملیات، لایه اکسید متشکل بر سطح فولاد را از بین می برد و باعث بهبود چسبندگی پوشش به سطح فولاد می شود. این نمونه ها به عنوان کاتد در نظر گیری شد. و از یک قطعه کبالت خاصل به ابعاد 5×20×20 میلی متر نیز به عنوان آند استفاده شد.
پوشش کامپوزیتی به وسیله دستگاه پتانسیواستات Sama500. با چگالی جریان 20 میلی آمپر، زمان 15 دقیقه و دمای 45 درجه سانتی گراد روی اتصال دهنده فولادی رسوب می دهند. فرآیند آبکاری در محلول واتس کبالت با ترکیب بهینه انجام شد. سوب دهی کبالت به روش آبکاری الکتریکی روی زیر لایه های مختلف و با استفاده از حمام های آبکاری متفاوتی انجام می شود. از جمله محلول هایی که برای آبکاری کبالت استفاده می شود. از جمله محلول هایی که برای آبکاری کبالت استفاده می شود.
می توان به محلول سیترات، محلول شامل تری اتیلین دی آمین و کلرید کبالت در 100 درصد هیدروکسید پتاسیم. محلول تیوسیانات کبالت دی دی متیل فرم آمید. کبالت در محلول آبی کلرید آمونیوم و محلول الکترولیت گلوکونات اشاره کرد. یکی از اولین محلول ها که برای رسوب دهی کبالت بکاری گیر شد.
توسط شخصی به نام واتس با ترکیب شیمیایی شامل: سولفات کبالت به عنوان ماده اصلی که حاوی یون های کبالت است. کلرید کبالت برای کمک به انحلال آند، کلرید سدیم برای بهبود هدایت یونی و اسید بیوریک به عنوان تنظیم کننده Ph است. این محلول برای آبکاری کبالت روی زیر لایه های فولادی استفاده می شود. و به حمام واتس کبالت معروف است. در جدول (2) ترکیب شیمیایی حمام آبکاری و شرایط عملکرد فرایند آبکاری نمایان و مشخص است. همه آزمایش ها در 100 میلی لیتر الکترولیت که با آب دیونیزه مهیا گردید، انجام شد. به منظور کنترل Ph از اسید سولفوریک و هیدروکسید آمونیوم استفاده شد.
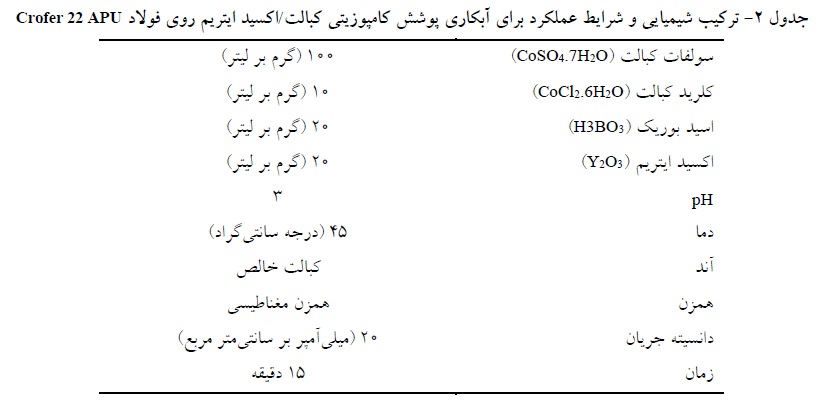
بعد از آبکاری، نمونه های پوشش دار و بدون پوشش. به مدت 500 ساعت در دمای 800 درجه سانتی گراد تحت اکسیداسیون همدما و هوای ساکن قرار گرفتند. وزن نمونه ها قبل و بعد از آزمون توسط ترازوی دیجیتال با دقت 6-10 گرم اندازه گیری شد. برای اطمینان از نتایج، آزمون اکسیداسیون همزمان روی سه نمونه مشابه انجام شد. برای بررسی مورفولوژی سطح نمونه ها و ضخامت پوشش و لایه های اکسیدی از میکروسکوپ الکترونی روبشی (SEM). و برای بررسی فازهای تشکیل شده در پوشش بعد از اکسیداسیون از الگوی پراش پرتو ایکس (XRD) استفاده شد.
آزمون چسبندگی به روش کراس کات برای تعیین میزان چسبندگی پوشش Co/Y2/O3 به زیر لایه فولادی انجام شد. این آزمون که روشی ساده و عملی برای ارزیابی چسبندگی سیستم های پوشش دهی تک و چند لایه است. طبق استاندارد ASTM D3359 (2017) صورت گرفت. ابتدا با ابزار برشی مناسب طرحی مشبک روی لایه پوششی تا رسیدن به زیر لایه ایجاد شد. و با برس در جهت قطری پنچ مرتبه روی برش های برش چسبانده و از روی سطح جدا شد. در نهایت ناحیه برش خورده با ذره بین نورانی تحت بررسی قرار گرفت.
فولاد Crofer 22apu
برای اندازه گیری مقاومت الکتریکی ویژه سطحی (ASR) نمونه های پوشش دار و بدون پوشش. از سیستمی استفاده شد که شماتیک آن در شکل (1) نمایان و کاملاً مشخص می باشد. برای این آزمون، خمیز و مش نقره محصول شرکت Full Cell materials آمریکا. به مساحت یک سانتی متر مربع روی نمونه های پوشش دار و نمونه های بدون پوشش قرار داده شد. سپس نمونه ها توسط این خمیر و مش نقره به سیم هایی از جنس نقره متصل شدند. که این سیم ها نقش اتصال دهنده نمونه به دستگاه اتولب را بازی می کردند. نمونه ها پس از مهیا سازی سطح و اتصال به سیم ها در یک کوره الکتریکی قرارگیری شدند.
و سر دیگر سیم های متصل به نمونه ها به دستگاه اتولب مدل Autolab Pgstat 302 متصل شد. از نرم افزار Nova 1.6 برای اجرای برنامه کرونوپتانسیو متری استفاده شد. در این برنامه جریان ثابت است. برای انجام این آزمون از جریان ثابت 500 میلی آمپر استفاده شد. خروجی اتولب که توسط نرم افزار ثبت می شود. ولتاژ است. با داشتن ولتاژ و جریان، مقدار مقاومتبه وسیله قانون اهم (V/I) محاسبه شد. بدین ترتیب با داشتن سطح نمونه ها و مقدار مقاومت اهمی، مقدار مقاومت الکتریکی سطحی محاسبه شد. اندازه گیری مقاومت الکتریکی سطحی بر حسب دما (800-650 درجه سانتی گراد). و زمان (200 ساعت در دمای 800 درجه سانتی گراد) در هوای ساکن در کوره الکتریکی انجام شد.
فولاد Crofer 22apu
3-نتایج و بحث
1-3- بررسی ریزساختار و ترکیب پوشش
شکل (2) تصویر میکروسکوپی الکترونی روبشی (شکل2-الف). و تحلیل طیف سنجی پراکندگی انرژی پرتو ایکس (EDS) (شکل 2-ب) پوشش ایجادی بر روی زیر لایه فولادی را نشان می دهد. همان گونه که در شکل (الف) مشاهده می شود. ذرات اکسید ایتریم به صورت یکنواخت و همگن در زمینه کبالت دچار پراکندگی شدند. پوشش اعمالی به طور کامل متراکم است و هیچگونه تخلخل و حفره ای در مقیاس بزرگ در آن نمایان و مشخص نیست.
تصاویر میکروسکوپ الکترونی روبشی از سطح نمونه های پوشش داده شده. توسط نرم افزار آنالیز تصویر ImageJ مورد بررسی قرار گرفت. و میانگین اندازه ذرات تقویت کننده در سطح پوشش 2/25 میکرومتر تعیین شد. میانگین اندازه ذرات تقویت کننده تقریباً 1/5 میکرومتر است. (شکل 3) که حاکی از اگلومره شدن ذرات Y2O3 در طی فرآیند آبکاری الکتریکی است.
شکل (4) تصویر میکروسکوپی الکترونی روبشی (شکل 4- الف). و تحلیل طیف سنجی پراکندگی انرژی پرتو ایکس (شکل4-ب) از مقطع عرضی نمونه مورد پوشش با کامپوزیت Co/Y2O3 را نشان می دهد. پوشش ایجادی چسبندگی کاملی به زیر لایه داشت و هیچ گونه تخلخل و جدایشی بین پوشش و زیر لایه مشاهده نمی شود. ضخامت پوشش متشکل روی تمام سطح زیر لایه فولادی تقریباً یکنواخت و برابر هفت میکرومتر تعیین شد.
2-3- چسبندگی پوشش به زیر لایه
شکل (5) نتایج آزمون چسبندگی به روش کراس کات را نشان می دهد.
نمایش تصویر سطح نمونه پوششی با Co/Y2O3 پس از این آزمون حاکی از آن است. که چسبندگی این پوشش بر اساس رده بندی استاندارد در کلاس 3B قرار دارد. یعنی پوشش در امتداد لبه ها و یا در محل های تقاطع برش های جدا گردید.
فولاد Crofer 22apu
و ناحیه جدا شده بیشتر از 5 درصد و کمتر از 15 درصد است. طبق استاندارد، این نتیجه به معنای این است که پوشش اعمالی چسبندگی مناسبی به زیر لایه فولادی دارد.
3-3- سینیتیک اکسیداسیون
به منظور مقایسه رفتار اکسیداسیون نمونه دارای پوشش و نمونه بدون پوشش. تغییرات وزن بر واحد سطح نمونه ها به عنوان تابعی از زمان اکسیداسیون اندازه گیری شد. هرچند استفاده از تغییر وزن برای تعیین مقاومت به اکسیداسیون آلیاژهای کروم دار در دماهای بالا. به دلیل تبخیر کروم، مقداری خطا را در تفسیر نتایج نشان می دهد. اما این نتایج بیشتر برای مقایسه رفتار اکسیداسیون نمونه ها استفاده می شوند. شکل (6-الف) تغییرات وزن ویژه و شکل (6-ب) مربع تغییرات وزن ویژه بر حسب زمان اکسیداسیون در 800 درجه سانتیگراد را نشان می دهد. بعد از 500 ساعت اکسیداسیون نمونه دارای پوشش تغییر وزنی برابر 0.45 میلی گرم. و نمونه بدون پوشش تغییر وزنی برابر 0.41 میلی گرم را از خود نشان می دهد.
با توجه به شکل (6-ب) می توان نتیجه گرفت که رفتار اکسیداسیونی این آلیاژ، هم به صورت پوشش دار. و هم به صورت بدون پوشش، با توجه به رابطه (1) از قانون سینیتیک پارابولیک پیروی می کند. زیرا بر طبق تئوری واگنر اگر نمودار مربع تغییرات وزن بر حسب دما یک خط راست باشد. نفوذ عناصر در لایه اکسیدی و یا پوشش، آهسته ترین فرایندی که نرخ اکسیداسیون را کنترل می کند. و تغییر وزن ماده مورد نظر از قانون پارابولیک تبعیت می کند.
که در آن δm تغییر وزن نمونه ها، A مساحت سطح نمونه ها، Kp ثابت نرخ پارابولیک،t زمان و C ثابت انتگرال است. که شروع سینیتیک پارابولیک را نشان می دهد. در اینجا دلیل رفتار پارابولیک نمونه های بدون پوشش و نمونه های دارای پوشش این است. که رشد لایه اکسید کروم متشکل روی نمونه ها از قانون پارابولیک تبعیت می کند.
مقادیر ثابت اکسیداسیون نمونه بدون پوشش از صفر تا 60 ساعت اکسیداسیون. برابر 5×13-10=Kp و از 50 تا 500 ساعت اکسیداسیون برابر 3×13-10=Kp است. نرخ اکسیداسیون بالاتر اولیه مربوطه به تشکیل پوسته اکسید کروم روی فولاد است. و پس از 50 ساعت اکسیداسیون با تشکیل پوسته اکسیدی نرخ اکسیداسیون کاهش می یابد. نرخ اکسیداسیون نمونه دارای پوشش هم در 100 ساعت ابتدایی اکسیداسیون بالاست (3×13-16=Kp).
دلیل این امر اکسیداسیون سریع کبالت است. که منجر به تشکیل اکسیدهای اسپینلی کبالت می شود. دلیل دیگری که می توان برای افزایش وزن بالای اولیه نمونه دارای پوشش با Co/Y2O3 (100 ساعت ابتدایی آزمون اکسیداسیون) ذکر کرد. اکسیداسیون همزمان پوشش و زیر لایه است. بعد این افزایش وزن سریع اولیه، مقدار افزایش وزن این نمونه با زمان اکسیداسیون به شدت کاهش می یابد. که دلیل این امر ایجاد یک لایه محافظ اکسیدی طی 100 ساعت ابتدایی فرآیند اکسیداسیون است.
با مقایسه زمان لازم برای تشکیل لایه محافظ اکسیدی در اثر اکسیداسیون پوشش اعمالی Co/Y2O3. با زمان لازم برای تشکیل لایه محافظ اکسیدی در پوشش هایی مانند MnCu و Ni-Co-Fe در شرایط کاری مشابه می توان گفت. سرعت تشکیل لایه اکسیدی در این پوشش بسیار بالاتر بوده و در کاهش نرخ اکسیداسیون نیز اثر بخشی بیشتری داشته است. کاهش نرخ اکسیداسیون پس از تشکیل این لایه اکسیدی محافظ نشان دهنده این است. که نفوذ اکسیژن به فصل مشترک فولاد و زیر لایه نیز به تأخیر افتاده است. که این در توافق با کار سایر پژوهشگران است.
فولاد Crofer 22apu
پس از 100 ساعت اکسیداسیون نرخ اکسیداسیون نمونه پوشش داده شده به شدت کاهش می یابد (8×14-10=Kp). این کاهش نرخ اکسیداسیون ناشی از تشکیل اکسید کبالت است. نرخ اکسیداسیون پایین، برای زمان های طولانی اکسیداسیون بسیار مهم است. زیرا نشان دهنده کاهش رشد لایه اکسید کروم است که مقاومت الکتریکی بالایی دارد. به طور کلی می توان گفت که محصول اکسیداسیون پوشش کبالت، نرخ رشد لایه اکسید کروم را کاهش داده است.
اکسید عناصر راکتیو سدهای مناسبی برای جلوگیری از تبخیر کروم نیستند. زیرا به طور معمول متخلخل و نازک هستند. بنابراین این اکسیدها نمی توانند عامل مناسبی برای جلوگیری از مسمومیت کاتد در سیستم های SOFC شوند. با وجود این حضور اکسید ایتریم در پوشش کبالت می تواند باعث افزایش چسبندگی پوشش به زیر لایه و نیز کاهش نرخ اکسیداسیون. و مقاومت الکتریکی سطحی نمونه پوشش داده شده در مقایسه با نمونه بدون پوشش شود.
4-3- ریزساختار و ترکیب شیمیایی نمونه های پس از اکسیداسیون بدون پوشش را پس از اکسیداسیون نشان می دهد.
فولاد Crofer 22apu
شکل (7) تصویر میکروسکوپی الکترونی روبشی از سطح نمونه
سطح نمونه بدون پوشش پس از 500 ساعت اکسیداسیون در هوا در 800 درجه سانتی گراد شامل یک لایه سیاه اکسیدی است. که روی این لایه دانه های هرمی شکل در جهت مرزدانه های لایه اکسیدی متشکل اند (شکل 7-الف). این دانه ها جزیره های کوچکی بر روی سطح نمونه تشکیل داده اند. نتایج تحلیل EDS از سطح نمونه نشان می دهد. که لایه سیاه رنگ شامل عناصر کروم، منگنز، اکسیژن و مقدار کمی عنصر آهن است. و دانه های هرمی شکل شامل عناصر کروم، منگنز و اکسیژن است (جدول 3). نتایج تحلیل پراش پرتو ایکس نشان می دهد. که لایه اکسیدی سیاه رنگ شامل اکسیدهای اسپینلی MnCr2O4 و FeCr2O4 است
. و ذرات هرمی شکل فقط رسوبات MnCr2O4 هستند (شکل 7). شکل (6-ب) سطح نمونه پوشش داده شده را بعد از 500 ساعت اکسیداسیون نشان می دهد که شامل ذرات هرمی شکل است. و علامت قابل توجهی از ترک و یا پوسته شدن در سطح آن دیده نمی شود. تحلیل پراش پرتو ایکس نشان می دهد که سطح نمونه پوشش داده شده بعد از اکسیداسیون شامل اکسیدهای اسپینلی MnCr2O4،MnCo2O4،Co3O4 و FeCr2O4 است (شکل8).
شکل (9) تصویر میکروسکوپی الکترونی روبشی و تحلیل پراش انرژی پرتو ایکس از مقطع عرضی مورد پولیش . نمونه های عاری از پوشش (شکل 8-الف و 8-ب) و مورد پوشش با کامپوزیت Co/Y2O3 (شکل 9-ج و 9-د) را نشان می دهد. در هر دو نمونه دو لایه روی زیر لایه فولادی مشاهده می شود. سطح نمونه بدون پوشش شامل یک لایه خارجی غنی از اکسید منگنز -کروم. و یک لایه داخلی غنی از اکسید کروم است که با نتایج سایر محققین مطابقت دارد.
ضخامت این لایه های اکسیدی همانطور که در شکل (9-الف) و (9-ب) نشان داده شده است. حدود سه میکرومتر است. تحلیل پراش پرتو ایکس تأیید می کند. که لایه داخلی اکسید کروم و لایه خارجی اکسید اسپینلی MnCr2O4 به علاوه مقدار کمی FeCe2O4 است (شکل 8). سطح نمونه پوشش داده شده نیز شامل یک لایه داخلی غنی از اکسید کروم و یک لایه خارجی غنی از اکسیدهای کبالت و منگنز-کبالت است. آنالیز نقشه عنصری از مقطع عرضی نمونه تشکیل این اکسیدهای اسپینلی را تائید می کند. ذرات Y2O3 که قبل از اکسیداسیون در سطح
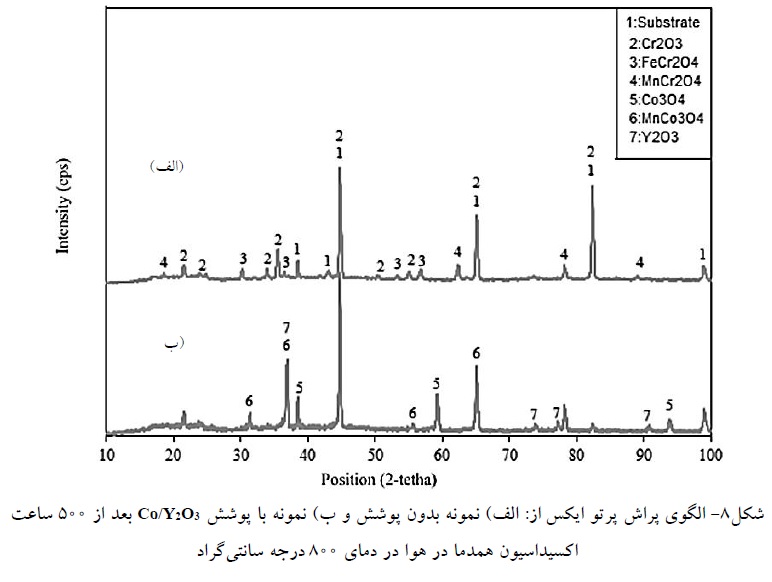
نمونه پوشش داده شده مشاهده می شدند. (شکل 3-الف) بعد از اکسیداسیون روی سطح قابل مشاهده نیستند (شکل 7-ب)، اما در داخل لایه اکسید کبالت خارجی معلوم و مشخص میشود (شکل 9-ج). زیرا این ذرات در اثر رشد لایه اکسید کبالت به دلیل نفوذ یون های فلزی و اکسیژن، در این لایه فرو رفته اند. و در تصویر مقطع عرضی پوشش قابل مشاهده هستند. توزیع عناصر ایتریم و اکسیژن در مقطع نمونه پوشش دهی می شود. که به وسیله آنالیز map عنصری در شکل های (10-د) و (10-و) معلوم و مشخص است. نیز وجود ذرات اکسید ایتریم را در مقطع عرضی پوشش اثبات می کند. لایه اکسید اسپینلی کبالت چسبندگی خوبی به لایه اکسید داخلی و نیز زیرلایه فولادی دارد (شکل 9-ج).
نفوذ عناصر در فصل مشترک پوشش و زیر لایه مسئله رایجی است. در تحقیقات مورد انجام توسط کروکاوا و جالانتا مشخص شد که منگنز. آهن و کروم می توانند از طریق مکانیزم نفوذ حجمی و از طریق مکانیزم مرزدانه. در اسپینل های Co و Mn-Cr و در دمای 800 درجه سانتی گراد نفوذ کنند. ابتدا همزمان با تشکیل پوشش Co/Y2O3، نفوذ Co از پوشش به زیرلایه و نفوذ Fe و Cr از زیرلایه به سمت پوشش رخ می دهد. اما مقدار نفوذ این عناصر بسیار کم است. Cr و Fe در طول مراحل اولیه اکسیداسیون نیز نفوذ می کنند.
که این امر منجر به مشاهد Fe در پروفیل لایه اسپینلی بعد از اکسیداسیون می گردد (شکل 9-د). آنالیز Map عنصری نیز نفوذ این عناصر را تأیید می کند (شکل 10). اما از آنجایی که انرژی آزاد منفی تشکیل اکسید کروم بیشتر از انرژی آزاد تشکیل اکسید آهن است. اکسید کروم پایدارتر از اکسید آهن است. بنابراین لایه Cr2O3 در فصل مشترک پوشش و زیرلایه تشکیل می شود. از سوی دیگر با توجه به اینکه ضریب نفوذ یون های فلزی در ترتیب DMn>DFe>DCr کاهش می یابد. به دلیل ضریب نفوذ بالاتر یونهای منگنز، از زیرلایه به سمت سطح فولاد لایه اسپینلی MnCr2O4 روی سطح لایه اکسیدی Cr2O3 تشکیل می شود. بنابراین فشار جزئی موضعی اکسیژن در اثر تشکیل MnCr2O4 و Cr2O3 بسیار کاهش یافته و برای تشکیل اکسید آهن بسیار کم است.
فولاد Crofer 22apu
مقایسه تصاویر شکل (9) نشان می دهد. که ضخامت لایه Cr2O3 تشکیلی روی نمونه بدون پوشش حدود دو میکرومتر است. در حالی که ضخامت لایه Cr2O3 تشکیلی روی نمونه مورد پوشش دهی حدود 700 نانومتر است. بنابراین لایه پوشش نرخ رشد لایه Cr2O3 را به حدود یک سوم کاهش می دهد. این لایه پوشش محافظ از نفوذ کروم به سمت خارج و نفوذ اکسیژن به سمت داخل فولاد جلوگیری کرده. و به همین دلیل نرخ رشد لایه اکسیدی Cr2O3 را کاهش می دهد . اثر اکسید عناصر اکتیو در کاهش رشد لایه اکسیدی Cr2O3. با توجه به اثر این عناصر بر افزایش مقاومت به اکسیداسیون فولادهای مشابه هنگامی که به عنوان پوشش روی این آلیاژها اعمال می شوند. توضیح داده می شود.
5-3- رفتار الکتریکی
پوشش مورد اعمال روی اتصال دهنده داخلی در پیل های سوختی اکسید جامد باید دارای مقاومت الکتریکی سطحی کمی باشد.
تا هدایت الکتریکی بین الکترودهای سلول های مجاور را افزایش دهد. بنابراین برای نشان دادن مفید بودن پوشش کامپوزیتی اعمال شده روی اتصال دهنده فولادی باید ثابت کرد. که این پوشش در شرایط کاری پیل های سوختی اکسید جامد، هدایت الکتریکی بالاتری در مقایه با نمونه بدون پوشش دارد. بدین منظور مقدار مقاومت الکتریکی سطحی نمونه ها بعد از 500 ساعت اکسیداسیون در هوا در 800 درجه سانتی گراد اندازه گیری شد. شکل(11) نمودار وابستگی مقاومت الکتریکی سطحی به دما را نشان می دهد. مقدار مقاومت الکتریکی سطحی با افزایش دما از 650 تا 800 درجه سانتی گراد کاهش می یابد. این رفتار مشابه رفتار مواد نیمه رساناست. که نشان می دهد هدایت الکتریکی با دما فعال می شود. مقدار مقاومت الکتریکی سطحی در این مواد با استفاده از رابطه (2) محاسبه می شود.
فولاد Crofer 22apu
که در آن A ثابت تناسب، T دما بر حسب کلوین. Ea انرژی اکتیواسیون برای هدایت از شیب نمودار (ASR/T) log بر حسب (T/1) محاسبه می شود (شکل 11). مقدار انرژی اکتیواسیون برای نمونه بدون پوشش برابر 26/22 کیلوژول بر مول و برای نمونه پوشش دهی شود. برای 11/53 کیلوژول بر مول به دست آمد. نمونه پوشش دهی میشود. در تمام محدوده های دمایی بررسی شده مقدار مقاومت الکتریکی سطحی کمتری از خود نشان می دهد. که این امر دلیلی بر اثر مفید پوشش اعمالی در جهت جلوگیری از تشکیل و رشد لایه های اکسیدی.
با مقاومت الکتریکی بالا مانند Cr2O3 است. دلیل مقدار مقاومت الکتریکی سطحی کمتر نمونه پوشش دهی میشود. تشکیل ترکیبات اسپینلی در طول فرآیند اکسیداسیون است. این ترکیبات اسپینلی که دارای ساختار مکعبی به صورت، A1+XB2-XO4 هستند. دارای آنیون های اکسیژن که مرکز وجود را پر می کنند. و کاتیون های A و B از عناصر مشابه دارای والانس های متفاوت نیز هستند. این کاتیون ها موقعیت های اکتاهدرال یا تتراهدرال را پر می کنند. بنابراین امکان انتقال راحت تر الکترون ها بین کاتیون های مجاور با والانس مشخص وجود دارد. این امر هدایت الکتریکی ترکیبات اسپینلی را افزایش می دهد. تحقیقات نشان می دهد که انرژی اکتیواسیون برای انتقال الکترون ها با جانشینی یون های چهار ظرفیتی شبیه منگنز کاهش می یابد.
بنابراین اگرچه وجود منگنز در پوشش ممکن است پارامتر شبکه و نفوذ سربالایی کروم را افزایش دهد. اما هدایت الکتریکی پوشش را افزایش می دهد. از سوی دیگر، کبالت یک عنصر نوع P است. که تأثیر مهمی روی افزایش هدایت الکتتریکی ترکیبات اسپینلی مانند MnCo2O4 شصت ثانیه بر سانتی متر. CoCr2O4 هفت و چهار دهم ثانیه بر سانتی متر و CoFe2O4 نود و سه صدم بر سانتی متر. در مقایسه با ترکیباتی مانند Cr2O3 دو صدم ثانیه بر سانتی متر.
و Mn,Cr) 3O4) پنچ دهم ثانیه بر سانتی متر برای MnCr2O4. و دو صدم ثانیه بر سانتی متر برای Mn1.2 Cr1.8O4 دارد. مقدار مقاومت الکتریکی سطحی کمتر نمونه پوششی در مقایسه با نمونه بدور از پوشش نشان می دهد. که ذرات Y2O3 عوامل مخربی برای هدایت الکتریکی پوشش نیستند و با کاهش نرخ اکسیداسیون نمونه پوشش می شدند. و بهبود چسبندگی پوشش به زیر لایه باعث افزایش هدایت الکتریکی نیز می شوند.
شکل (12) تغییرات مقاومت الکتریکی سطحی نمونه ها بر حسب زمان اکسیداسیون را در هوا در 800 درجه سانتی گراد نشان می دهد. مقدار مقاومت الکتریکی سطحی نمونه در تمام محدوده زمانی با افزایش زمان افزایش می یابد. بعد از 200 ساعت اکسیداسیون، مقدار مقاومت الکتریکی سطحی برای نمونه بدون پوشش برابر 25/9 میلی اهم بر سانتی متر مربع. و برای نمونه مورد پوشش برابر 15/8 میلی اهم بر سانتی متر مربع است. بایستی توجه داشت که مقدار مقاومت الکتتریکی سطحی یک اتصال دهنده فلزی پوشش داده شده.
با یک پوشش محافظ تحت تأثیر لایه پوشش و لایه اکسیدی که در فصل مشترک فلز و پوشش. در طی شرایط کاری پیل های سوختی اکسید جامد تشکیل می شود، است. بنابراین یکی از عوامل مهمی که باعث کاهش مقاومت الکتریکی سطحی نمونه پوشش داده شده است. ضخامت کمتر لایه اکسیدی Cr2O3 در این نمونه (حدود 700نانومتر) در مقایسه با نمونه بدون پوشش (حدود دو میکرومتر) است. زیرا این لایه اکسیدی مقاومت الکتریکی بالایی دارد. به طور کلی مقدار مقاومت الکتریکی سطحی کمتر نمونه مورد پوشش نشان می دهد که تأثیر مثبت پوشش اعمالی روی اتصال دهنده فولادی است.
4- نتیجه گیری
1- پوشش کامپوزیتی Co/Y2O3 با چسبندگی خوب روی فولاد زنگ نزن فریتی Crofer 22APU به روش آبکاری الکتریکی با جریان مستقیم تشکیل شد.
2- پوشش اعمالی باعث کاهش نرخ خوردگی فولاد Crofer 22APU. در محدوده 100 تا 500 ساعت اکسیداسیون در هوا در دمای 800 درجه سانتی گراد شد.
3-یک پوسته اکسیدی دو لایه روی نمونه پوشش داده شده با Co/Y2O3. بعد از 500 ساعت اکسیداسیون در هوا در دمای 800 درجه سانتی گراد تشکیل شد. که لایه داخلی آن شامل عناصر کروم و اکسیژن و لایه خارجی آن شامل عناصر کبالت، کروم، منگنز، اکسیژن، آهن و ایتریم بود.
4- تحلیل پراش انرژی پرتو ایکس نشان داد که ضخامت پوسته اکسیدی Cr2O3. در نمونه بدون پوشش حدود سه برابر نمونه دارای پوشش می گردد.
اندازه گیری مقدار مقاومت الکتریکی سطحی نمونه ها بر حسب دما نشان داد که نمونه ها رفتاری مشابه مواد نیمه رسانا دارند. و همواره مقدار مقاومت الکتریکی سطحی نمونه پوشش داده شده کمتر از نمونه بدون پوشش است.
فاطمه سعید پور، مرتضی زند رحیمی، هادی ابراهیمی فر.
1- دانشکده مهندسی مواد، مجتمع آموزش عالی فنی و مهندسی اسفراین. 2-دانشکده مهندسی مواد، دانشگاه شهید باهنر کرمان. 3-دانشکده مهندسی مکانیک و مواد، دانشگاه تحصیلات تکمیلی صنعتی و فناوری پیشرفته
مواد پیشرفته در مهندسی، سال 38، شماره 1،بهار 1398
شرکت خشکه و فولاد پایتخت (( مدیریت : جواد دلاکان )) صنعتگران عزیز، افتخار داریم. که سی سال تجربه گرانبهای خویش را در زمینه عرضه انواع ورق آلیاژی. و انواع فولاد آلیاژی برای خدمت رسانی به شما هموطنان کشور عزیزمان ایران ارائه می دهیم. پیشاپیش از اینکه شرکت خشکه و فولاد پایتخت را جهت خرید خود انتخاب می نمایید سپاسگزاریم.ارتباط با ما:
۰۹۱۲۱۲۲۴۲۲۷
۰۹۳۷۱۹۰۱۸۰۷
تلفن: ۰۲۱۶۶۸۰۰۲۵۱
فکس: ۶۶۸۰۰۵۴۶
ارتباط با ما در شبکه های اجتماعی
https://t.me/foolad_paytakht تلگرام
https://www.instagram.com/folad_paytakht اینستاگرام
https://www.instagram.com/foolad_paytakht.ir اینستاگرام